坩埚浇铸口核心机制解析
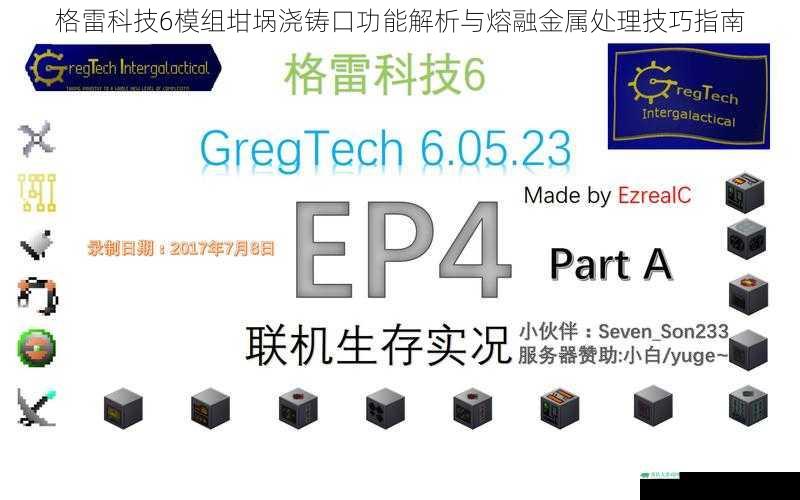
格雷科技6(GregTech 6)模组中的坩埚浇铸口(Crucible Pouring Spout)是冶金系统的核心组件,其功能实现基于复杂的流体力学模拟与热力学计算。该装置通过双层结构设计实现精准控制:上层的耐高温陶瓷内衬(耐温阈值1800K)负责承载熔融金属,下层的机械传动装置通过红石信号控制闸门开合角度,实现每秒200-1500mB的流速调节。
浇铸口与模具的联动机制遵循体积匹配原则。当检测到模具空置且容积大于当前流体储量时,浇铸口将自动终止浇注流程。对于铸造盆(Casting Basin)这类开放式容器,系统会持续注入金属直至达到预设体积阈值。值得注意的是,与流体罐(Fluid Tank)对接时,浇铸口会激活压力平衡模式,通过内置的真空补偿装置防止虹吸效应。
金属相变控制关键技术
熔融金属的凝固判定基于三维热传导算法:模具材质导热系数(铜制模具为56 W/m·K,钢制模具为43 W/m·K)与环境温度共同决定冷却速率。建议在铸造高熔点金属(如钨,熔点3422°C)时采用预热策略,将模具加热至800°C以上可有效避免表面龟裂。
多金属顺序浇注需遵循凝固点梯度原则。例如在制作红石合金线路板时,应先注入熔点较高的退火铜(1084°C),待其形成凝固层后再注入液态红石(600°C)。逆向操作会导致红石成分气化,造成材料损失和模具污染。
流体交互规则与风险管控
金属混合防护机制基于元素亲和度数据库运作。当检测到两种不兼容金属接触时(如铝与铁),系统会触发紧急排放协议。建议在产线布局阶段预留安全缓冲池,容量应达到单次最大浇注量的150%。对于必须进行的合金化操作(如青铜冶炼),需确保锡与铜的比例严格控制在1:3至1:4之间,偏差超过±5%将显著降低成品机械强度。
温度波动补偿是维持浇铸质量的关键。当环境温度低于金属熔点的80%时,建议启用辅助加热线圈(耗能3-5kEU/t)。对于露天作业场景,需配置气象监测模块,风速超过8m/s时将自动启动防风罩。
高效浇注操作规范
模具预处理应分三个阶段实施:初次使用需进行退火处理(保持600°C恒温30分钟),日常使用前进行表面氧化层清除(砂纸打磨至Ra≤3.2μm),长期停用时应涂覆石墨隔离剂。复杂构件的分层铸造需注意结晶方向控制,推荐采用螺旋浇注路径以提高材料致密度。
浇铸口维护周期与处理金属种类直接相关:处理钢水时每10次操作需检查陶瓷内衬,处理锇金属时维护间隔缩短至3次。建议建立数字化的维护日志系统,记录每次操作的金属类型、温度峰值和流速参数。
自动化集成方案
红石控制系统的信号延迟必须控制在2tick以内,否则会导致金属溢出。推荐使用三级联控方案:初级传感器监测流体存量,次级控制器调节阀门开度,三级安全模块监控系统完整性。计算机模组(如OpenComputers)的脚本编写需包含熔池震荡监测算法,当检测到流体表面波动幅度超过3mm时自动降低流速。
能源优化方面,建议将浇铸操作集中在电网负荷低谷时段。采用智能功率分配器可将峰值能耗降低40%,配合飞轮储能装置(容量≥500kEU)可确保连续浇注作业的稳定性。
事故应急处理预案
金属凝固堵塞的解决方案需分情况处理:当堵塞发生在浇铸口颈部时,启用反向气压脉冲(0.5-0.8MPa)进行疏通;模具内凝固则需使用定向加热器(功率≥128EU/t)进行局部熔解。建议常备液态氮应急包,用于快速冷却失控的熔融金属流。
通过精准掌握坩埚浇铸口的工作原理并严格执行操作规范,玩家可显著提升冶金系统的安全性和生产效率。建议在实际操作中建立质量追溯体系,持续优化工艺参数以适应不同生产需求。