车削加工是机械制造领域的核心技术之一,涉及金属、塑料等材料的精密成型。对于初学者而言,掌握车床操作的核心逻辑与技巧是快速提升的关键。将系统解析车削加工的完整知识体系,帮助新手建立科学的操作框架。
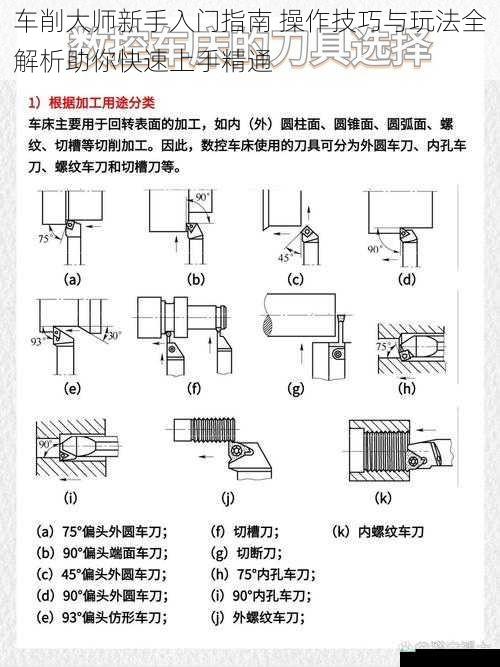
车床结构与安全规范认知
1.1 车床核心组件功能解析
现代数控车床由主轴箱、进给系统、刀塔、尾座、控制系统五大模块构成。主轴箱通过变频电机驱动工件旋转,转速范围通常为50-4000rpm,具体数值取决于工件直径与材料特性。刀塔采用伺服电机驱动,定位精度可达±0.005mm,支持12-24工位自动换刀。
1.2 安全操作黄金法则
(1)防护装备必须包含ANSI认证的防护眼镜(透光率≥89%)及防滑工作鞋(抗压等级≥200J)
(2)开机前执行"三点检查法":冷却液位(不低于容积的2/3)、导轨润滑(油膜厚度0.02-0.03mm)、卡盘夹紧力(直径50mm工件需≥300N·m)
(3)紧急制动训练要求操作者在0.5秒内能触达急停按钮,建议每周进行模拟演练
刀具系统与工艺参数优化
2.1 刀具选择矩阵
针对不同加工场景,需建立四维选型模型:
2.2 切削参数动态平衡
建立Vc(切削速度)=π×D×n/1000的数学模型,结合材料加工性指数(以45钢为基准1.0)进行调整。例如铝合金切削速度可提升至200-300m/min,不锈钢则应降至50-80m/min。进给量f建议控制在0.1-0.3mm/r区间,精加工时采用递减策略。
精密加工操作技巧
3.1 工件装夹艺术
三爪卡盘装夹需遵循"三点接触"原则,对于L/D>4的细长轴,必须配合中心架使用。薄壁件加工推荐液压膨胀夹具,夹持力波动可控制在±5%以内。精密套筒类零件建议采用热装法,加热温度T=Δ/(α×D)+20℃,其中Δ为过盈量,α为材料膨胀系数。
3.2 对刀与补偿技术
激光对刀仪可将对刀时间缩短至传统方法的1/3,精度达±0.002mm。刀具磨损补偿建议每加工50件检测一次,X向补偿量ΔX=VB×tan(主偏角),其中VB为后刀面磨损量。热变形补偿需建立温度-位移曲线,通常Z向补偿量约0.01mm/℃。
典型问题诊断与解决
4.1 振刀现象控制
当振幅超过0.02mm时应启动抑振程序:
(1)检查系统刚度:刀杆悬伸比≤4:1
(2)优化切削参数:降低转速10-15%或提高进给20%
(3)采用变转速切削:设置±5%的转速波动频率
4.2 尺寸精度超差溯源
建立尺寸链分析模型,重点检测:
进阶技能提升路径
建议新手按照"基础操作(50小时)→参数优化(100小时)→特殊材料加工(200小时)"的三阶段训练法。掌握恒线速切削、螺纹复合加工等高级功能后,可尝试宏程序编写,实现个性化加工方案。定期参加技能比武,通过对比0.01mm级精度的工件,可快速提升质量意识。
车削技术的精进永无止境,建议建立个人加工数据库,记录每次工艺参数与加工效果的对应关系。随着经验积累,可逐步发展出适应特定场景的优化算法,最终形成独特的加工风格。切记,安全规范与基础理论的持续学习,是通向大师之路的基石。